I. Introduction
In the realm of metal sheet and mechanical engineering, the press brake is a key tool for transforming sheet metal into intricate shapes and designs. This powerful machine can achieve precise bending and folding, utterly change the industry, and create mass products ranging from simple rackets to complex mechanical components.
However, as every coin has two sides, it has restrictions too. Our passage aims to introduce the press brake advantages and disadvantages in detail, making you understand the press brake comprehensively in the metal sheet industry.
II. Types of Press Brake

Mechanical press brake
This is the most common type of press brake. The mechanism is operated by the electric motors inside them. The motor offers energy to the flywheel and rotates the big flywheel at high speed. The operator controls the flywheel via the clutch.
The mechanical press brake is simple to operate especially in electronic equipment. It makes maintenance and operation easier. Once the ram is connected, it must undergo the whole process. If the gate stroke is too large, the press brake may be locked, which is a potential hazard.
- Pros: low cost, easy operation
- Cons: restrictions on precision, power, and control
Hydraulic press brake
The hydraulic press brake uses hydraulic to push the oil cylinder down instead of a mechanical setting. It can be equipped with multiple cylinders, which provides much convenience for operators to control the elbow, thus achieving high custom and precise bending.
Compared with the mechanical press brake, the hydraulic press brake offers more accurate bending and better control. It can be easily adjusted to fit various thicknesses of metal and achieve intricate bending at steady movement. It is usually more expensive but is popular because of its higher performance and versatility.
- Pros: higher precision, control, and force, and fits various materials
- Cons: high cost, more complex operation and can’t exceed its rated tonnage
CNC press brake
The CNC press brake is highly custom and accurate and is controlled by computer technology to improve efficiency and control accuracy. The skilled operators can input the data like bending angle, sheet thickness, and width to the controller to control the machine.
- Pros: high accuracy and precision, easy operation and handle various shapes and angles
- Cons: high cost, limitations with highly reflective or brittle materials
III. Press Brake Advantages
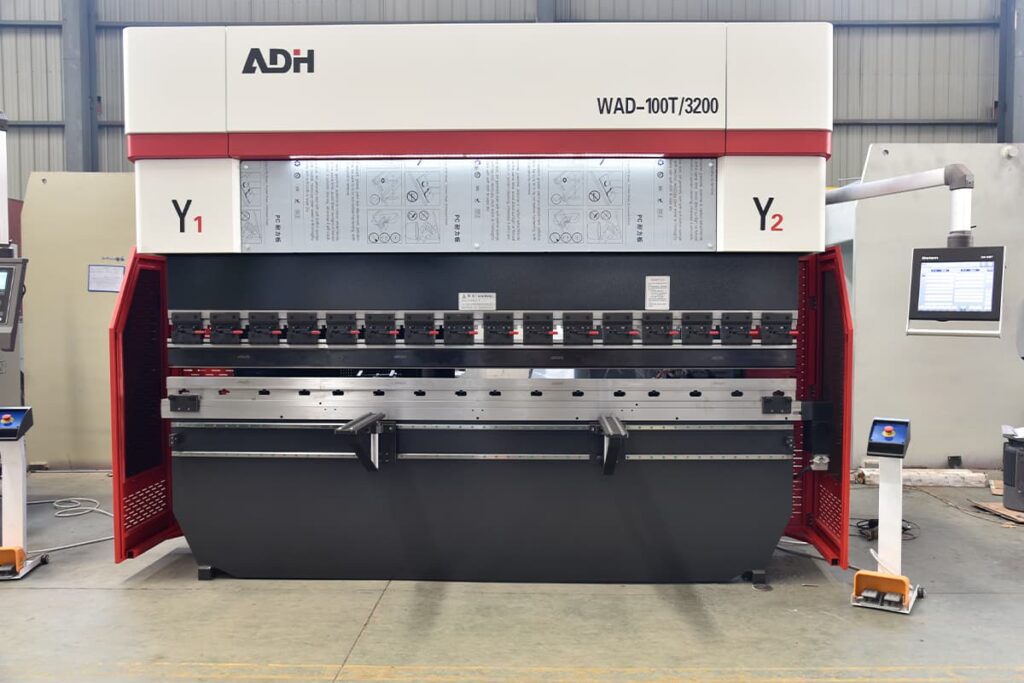
Precision and Accuracy
Reduced Material Waste
Accurate bending minimizes material waste by ensuring each bend meets the required specifications. This reduces the need for rework and scrap, leading to cost savings and more efficient use of materials.
Enhanced Product Quality
High precision and accuracy result in consistent product quality. Components bent to exact specifications fit together better and perform as intended, which is crucial in industries like aerospace, automotive, and electronics.
Increased Production Efficiency
The ability to produce accurate bends consistently reduces downtime and increases throughput. Operators spend less time making adjustments and corrections, allowing for faster production cycles and higher overall efficiency.
Versatility
Material Compatibility
Press brakes are compatible with a wide range of materials, including various grades of steel (e.g., mild steel, stainless steel), aluminum alloys (e.g., 6061, 5052), copper, and exotic alloys like titanium and Inconel. This broad material compatibility allows manufacturers to use press brakes for diverse projects without needing multiple specialized machines.
Complex Bending Operations
Press brakes can perform complex bends, not just simple right-angle bends. They can execute intricate shapes and multi-step bending sequences, essential for creating sophisticated components. This capability is crucial in sectors like aerospace and electronics, where precision and complexity are paramount.
Tooling Flexibility
The versatility of press brakes is further enhanced by their tooling flexibility. A wide array of dies and punches can be used to achieve various bending profiles and angles. Operators can quickly switch between different tooling setups, allowing for rapid adaptation to new tasks.
This flexibility is particularly advantageous in custom fabrication shops, where handling diverse projects efficiently is a key competitive advantage. For instance, V-dies, offset dies, and hemming dies can all be used in different configurations to create specific bends.
Integration with Automation
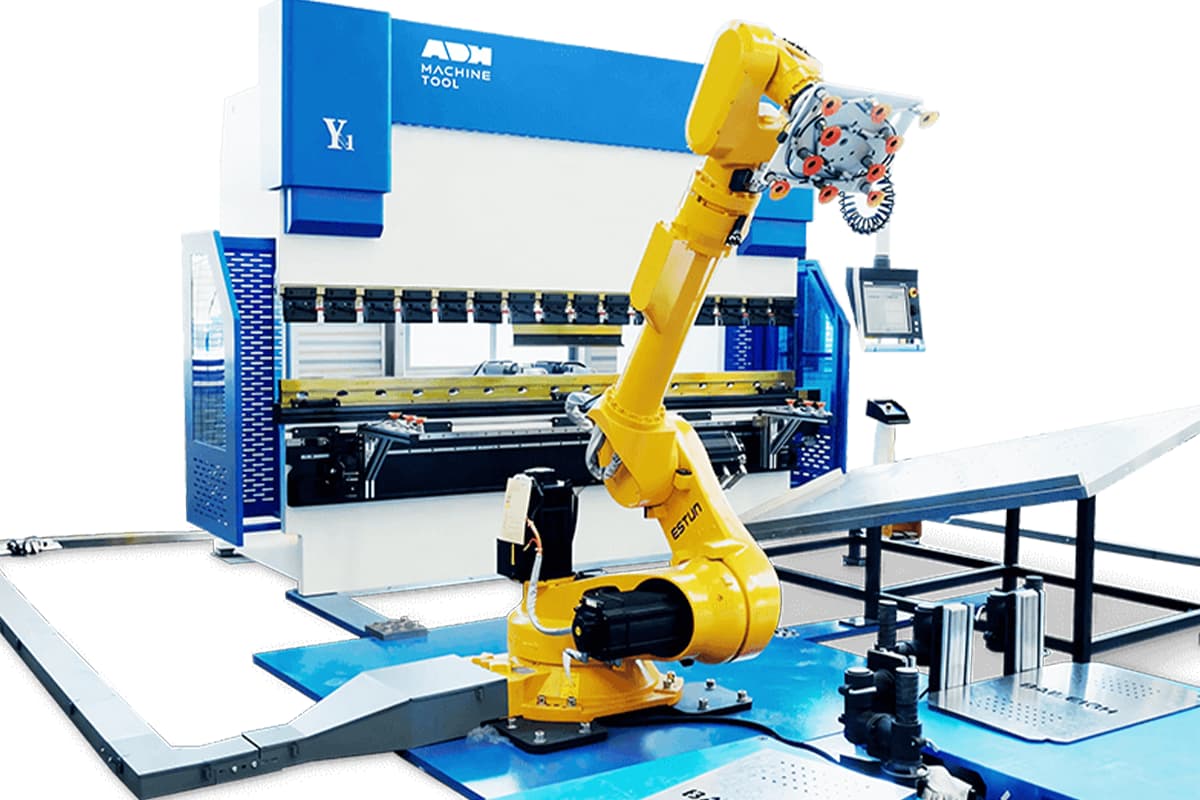
Modern press brakes can be integrated with automated systems, such as robotic arms and conveyor belts, to streamline production processes. This integration enhances versatility by enabling continuous operation and reducing manual intervention.
In high-volume manufacturing environments, automated press brakes can operate around the clock, producing consistent bends with minimal human oversight. This not only increases efficiency but also ensures high-quality output.
Customization and Programming
Advanced press brakes equipped with CNC (Computer Numerical Control) systems offer extensive customization and programming capabilities. Operators can input specific parameters and create custom bending sequences tailored to unique project requirements. This feature is invaluable in industries where bespoke components are the norm.
Efficiency and Speed
Enhancing Production Speed
Press brakes significantly enhance production speed, a critical factor in high-volume manufacturing environments. Modern press brakes, equipped with advanced CNC (Computer Numerical Control) systems, allow for rapid setup and swift transitions between different bending operations. This capability minimizes downtime and maximizes throughput, enabling manufacturers to meet tight production schedules.
Automation and Process Optimization
Automation plays a crucial role in improving the efficiency and speed of press brake operations. Integrating press brakes with automated systems, such as robotic arms and conveyor belts, allows for continuous operation with minimal human intervention.
This speeds up the production process and reduces the likelihood of human error, leading to higher consistency and quality. In high-mix, low-volume production environments, automation enables quick adaptation to different production requirements, ensuring that diverse parts are produced efficiently.
Reducing Setup Times
Modern press brakes excel in reducing setup times. CNC systems allow operators to program specific parameters and save these settings for future use, drastically cutting down the time required to set up the machine for different tasks.
Programmable backgauges and quick-change tooling systems further enhance this capability, allowing operators to switch between different bending operations in minutes. In the electronics manufacturing industry, where rapid changes between different product lines are common, this feature is particularly beneficial.
Minimizing Material Waste
Efficiency in press brake operations is also achieved by minimizing material waste. The precision of CNC-controlled press brakes ensures that each bend is made to exact specifications, reducing the need for rework and scrap. This not only saves material costs but also speeds up the production process by eliminating the time spent correcting errors.
Increasing Throughput
The combination of high speed and precision in press brake operations leads to increased throughput. By ensuring that each bend is made accurately and quickly, press brakes can produce more parts in a shorter amount of time. This is essential in industries with high demand, such as construction and automotive manufacturing.
Real-Time Monitoring and Adjustments
Advanced press brakes are equipped with real-time monitoring systems that track the bending process and make adjustments as needed. Laser and optical sensors measure the position and angle of the metal sheet during bending, providing immediate feedback to the CNC system.
This allows for on-the-fly corrections, ensuring that the final product meets the required specifications without manual adjustments. This feature is particularly valuable in precision-dependent industries like aerospace and electronics, where even minor deviations can have significant consequences.
Energy Efficiency
Modern press brakes, especially servo-electric models, are designed to be energy-efficient. They use electric motors and ball screws to drive the ram, reducing energy consumption compared to traditional hydraulic systems.
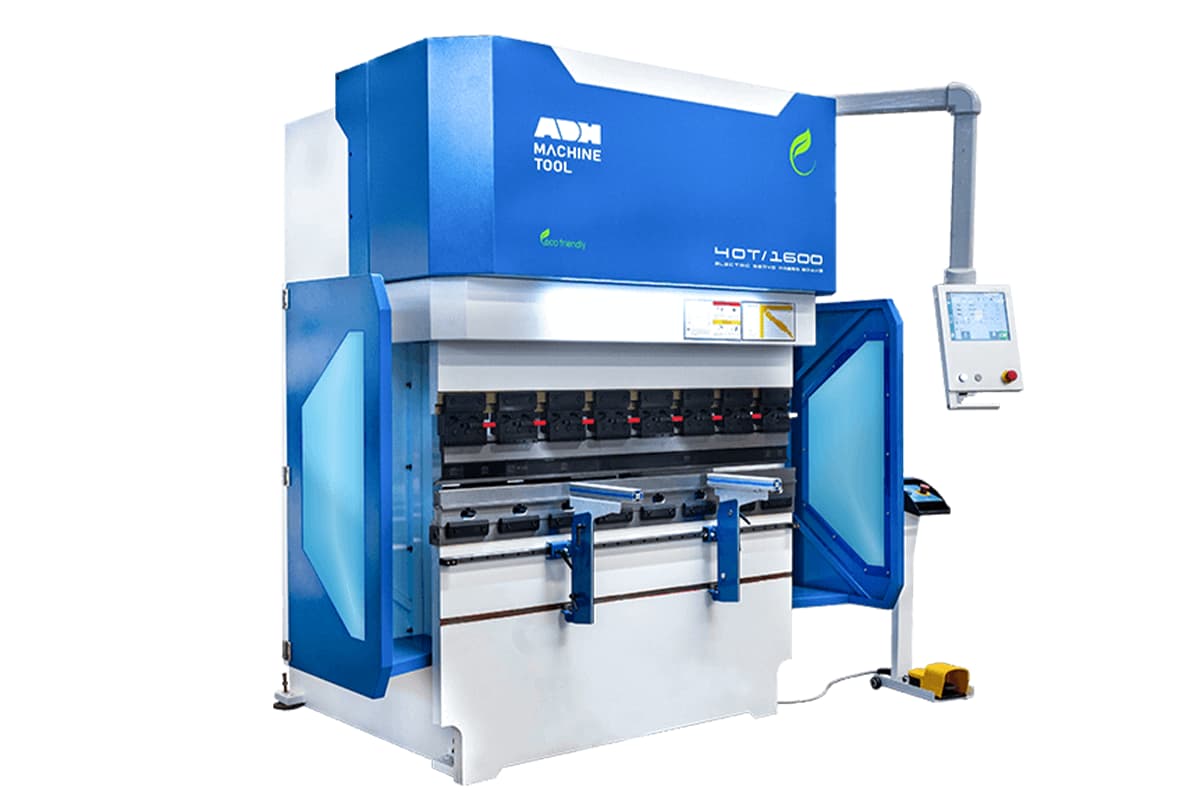
This not only lowers operational costs but also contributes to a more sustainable manufacturing process. In industries where energy costs are a significant concern, such as large-scale metal fabrication, the energy efficiency of press brakes can lead to substantial savings.
Cost-Effectiveness
Long-Term Savings
Investing in a press brake can result in substantial long-term savings for manufacturers. While the initial purchase cost of a high-end press brake, especially those with CNC systems, can be significant, the reduction in material waste, labor costs, and rework expenses over time offsets this initial investment.
The precision and repeatability of press brakes ensure that each bend meets exact specifications, reducing the likelihood of errors and the associated costs of reworking or scrapping faulty parts.
Reduced Labor Costs
Modern press brakes are designed to be user-friendly, which minimizes the need for highly skilled labor. While some training is required, especially for CNC models, the learning curve is not steep.
The ease of operation means that a smaller, less specialized workforce can efficiently operate these machines, leading to lower labor costs. Additionally, the automation capabilities of advanced press brakes further reduce the need for manual intervention, allowing operators to focus on other tasks.
Low Maintenance Costs
Regular maintenance is necessary to keep press brakes functioning optimally, but the maintenance costs are relatively low compared to other heavy machinery. Modern press brakes, especially servo-electric models, have fewer moving parts and do not require hydraulic fluids, reducing the frequency and cost of maintenance.
Hydraulic press brakes, although requiring routine checks and fluid changes, are designed for durability and long-term reliability. A maintenance schedule that includes regular inspections and timely repairs can prevent costly downtime and extend the machine's lifespan.
Energy Efficiency
Servo-electric press brakes are known for their energy efficiency, consuming less power than traditional hydraulic models. This reduction in energy consumption not only lowers operational costs but also contributes to a more sustainable manufacturing process.
In industries where energy costs are a significant concern, such as large-scale metal fabrication, the energy efficiency of press brakes can lead to substantial savings.
Longevity of Tooling
The tooling used in press brakes, such as dies and punches, is relatively inexpensive and has a long lifespan. High-quality tooling maintains its dimensions and alignment over extended periods, ensuring consistent bending results and reducing the need for frequent replacements.
This longevity contributes to the overall cost-effectiveness of press brake operations, as the initial investment in tooling is amortized over many production cycles.
Versatility in Production
The versatility of press brakes allows manufacturers to handle a wide range of projects with a single machine, reducing the need for multiple specialized machines. This adaptability not only saves on equipment costs but also enhances operational efficiency by allowing quick transitions between different bending operations.
The ability to produce various parts, from simple bends to complex shapes, using the same press brake makes it a cost-effective choice for manufacturers with diverse production requirements.
Safety

Modern press brakes are equipped with advanced safety features designed to protect operators and ensure a safe working environment.
- Laser sensors detect the position of the operator's hands and the metal sheet during the bending process. If an obstruction is detected in the danger zone, the machine stops immediately.
- Light curtains create an invisible barrier around the operating area. If this barrier is breached, the machine stops instantly, ensuring that operators cannot accidentally place their hands or other body parts in the danger zone while the machine is running.
- Dual-hand control systems require operators to use both hands to initiate the bending process. This ensures that their hands are away from the bending area, significantly reducing the risk of accidental injuries.
Modern press brakes are designed with ergonomics in mind to reduce operator fatigue and the risk of repetitive strain injuries.
- Adjustable workstations allow operators to position the metal sheet and tooling at a comfortable height, reducing strain on their backs and arms.
- User-friendly interfaces, including intuitive touchscreens and programmable controls, make it easier for operators to set up and control the press brake, reducing the likelihood of errors and accidents.
Automated press brake systems also incorporate safety features to protect operators and ensure safe operation.
- E-stop buttons are strategically placed around the press brake for quick access from any position. Pressing the E-stop button stops the machine immediately, preventing further operation until the issue is resolved.
- When integrating press brakes with robotic systems, safety protocols must be established to prevent accidents. This includes defining safe zones, implementing fail-safe mechanisms, and ensuring that robots operate within controlled parameters.
- Safety fencing creates a physical barrier around automated press brake systems, preventing unauthorized access to the operating area and ensuring that only trained personnel can interact with the machine.
Ease of Operation
Modern press brakes are designed with user-friendly interfaces, making them accessible even to operators with minimal experience. CNC press brakes allow operators to program complex bending sequences easily.
While some training is necessary to operate CNC press brakes, the learning curve is not steep. Automation features in modern press brakes enhance ease of operation by reducing the need for manual intervention.
Advanced press brakes are equipped with real-time monitoring systems that track the bending process and make necessary adjustments. Modern press brakes are designed with high error tolerance, allowing operators to recover quickly from mistakes.
IV. Press Brake Disadvantages
High initial cost:Â the press brake needs mass initial investment due to purchase and maintenance. Also, the machine requires specialized equipment and training, which may increase the initial cost of setting up the machine operation. It needs more energy and may improve the operation cost apparently. The press brake with automatic is expensive, which can reduce the small company to order High-end models.
Material size and thickness limitations: press brakes have limitations regarding the size and thickness of materials they can handle. A Texas-based fabricator found that their press brake could not efficiently bend very thick steel plates, necessitating additional investments in specialized tooling and equipment. This limitation can restrict the variety of projects a press brake can undertake, adding complexity and cost.
Require high pressure:Â press brake needs high pressure to operate. This means press brake may be not suitable for thin materials due to high pressure may cause material deformation. Besides, the high pressure is dangerous. The press brake must be operated by skilled operators to use, thus the potential risks may be reduced.
Restricted to simple geometries:Â press brakes are also limited in the geometries they can create. Although they can create simple bends, they cannot create more complex shapes such as curves or spirals. Thus, if complex geometrical shapes need to be created, different methods may be required, such as stamping or hydroforming.
Need professional training:Â the press brake can be safely and effectively operated by professional training. The operator must receive proper training to know the working principle of the machine and how to set the material correctly. Additionally, the operators must know the related risks to high-pressure operations and how to escape injury.
Space requirement: the press brake has large sizes, thus more workshop area must be spared for machine placement, also including safety zones around the machine. A manufacturing company in New York struggled with space constraints when they introduced a large hydraulic press brake. The machine's footprint, along with the necessary space for material handling and operator movement, forced them to reorganize their entire workshop, which disrupted their production flow.
Noise and vibration:Â there may be some noises produced when the press brake is operated. Thus, the operator needs an ear-protective device. Also, it can rouse vibration on the working spot.
Maintenance:Â the press brake needs regular maintenance and should be often cleaned to ensure the quality of products. Hydraulic press brakes, in particular, require routine checks and fluid changes, demanding skilled technicians and adding to operational costs.
Safety concerns: Operating press brakes involves inherent safety risks. A workshop in Texas reported an incident where a mechanical press brake locked due to the ram traveling too far, posing a safety hazard. High pressure during bending operations can also be dangerous, especially with thin materials that may deform or break. Ensuring strict adherence to safety protocols and regular maintenance is essential to minimize risks.
Risk of breaking during bending:Â during the bending process, the edges and corners of the material will develop burrs or oxide layers, which may cause the material to crack or break during the bending process.
Spring-Back Issues: spring-back is a common issue in press brake forming, where the material tends to return to its original shape after bending. This phenomenon can impact the accuracy of the final product, necessitating additional adjustments and processes.
V. FAQs
1. What materials can a press brake handle?
Press brakes are versatile machines capable of handling a wide variety of materials. Commonly processed materials include stainless steel, carbon steel, aluminum, copper, and brass. Additionally, press brakes can manage more exotic materials such as titanium and specialized alloys, provided they fall within the machine's tonnage capacity and bending capabilities.
2. What are the maintenance requirements for a press brake?
Maintaining a press brake involves routine inspections and servicing to ensure it operates efficiently and safely. Key maintenance tasks include lubricating moving parts, inspecting hydraulic systems, checking for wear on tooling, and ensuring proper alignment and calibration.
Regular maintenance routines help in preventing unexpected downtimes and extending the machine's lifespan. It's also important to follow the manufacturer's recommended maintenance schedule and guidelines closely.
3. Can press brakes be automated?
Yes, press brakes can be automated, especially modern CNC press brakes that offer advanced automation options. These machines can be integrated with robotic arms, automated material handling systems, and advanced software for programming and monitoring.
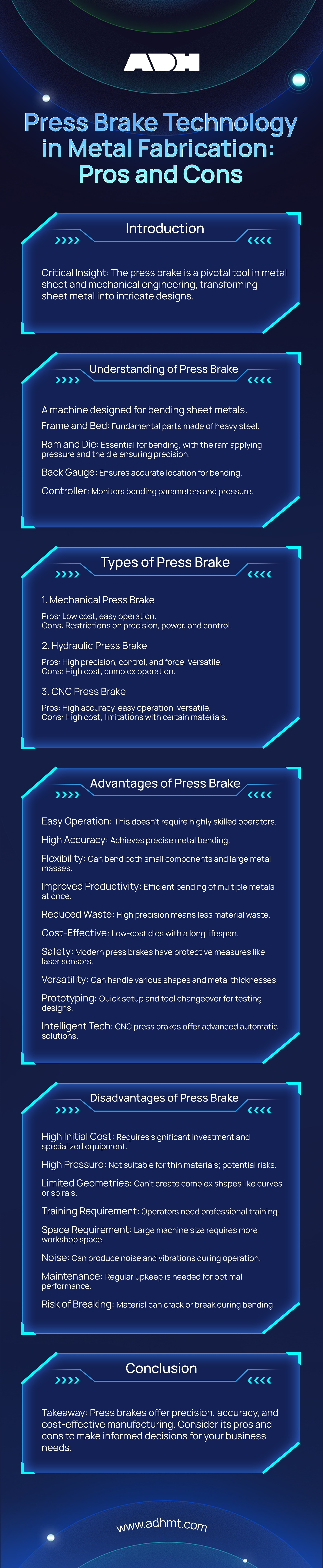
Download the Infographic With High Resolution
Silicone Rubber Sheet,Round Buckle Rubber Sheet,Non-Slip Rubber Sheet,High Elastic Rubber Sheet
HEBEI JIEXING RUBBER SEALS CO.,LTD , https://www.jiexingrubber.com