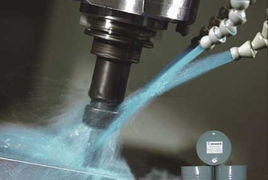
Below we briefly analyze the following factors:
Equipment: Equipment is often the first element in the selection of left and right fluids, because each equipment was originally designed to use pure oil or waterborne products. In addition, the type of equipment also determines the choice of processing fluid, because different types of equipment often determine the processing method of this equipment and the workpiece that can be processed.
Tool: This may be more easily overlooked by everyone. Because of problems that occur during the processing, we often think of whether it is a material problem or a fluid problem. In fact, many problems in the machining process are caused by tools. For example, if you use a coated knife to process at a high speed and you want to make a very good finish, it is often impossible to do so, but the light knife will work better.
Machining materials: This we all think, because different materials have different characteristics, there are different requirements for processing. No one will use the active sulfur-containing processing fluid to process copper.
Processing method: It is often seen that the salesman said that processing aluminum alloy is very simple, because the hardness of aluminum alloy is not high. I instantly thought of blind people's images. Frozen tofu can kill people! In the same material, broaching and grinding are absolutely different.
Spindle speed of the equipment: For newcomers to this line, they may know that there are only 1500 rpm for stainless steel turning and some 10,000 rpm for high precision milling of aluminum alloys. But why set this speed? This can be found on the fire and sticky knife customers to talk about this matter.
Feed rate: A very important information point. Sometimes customers may think your cutting fluid is not well lubricated, or the heat is not good enough. This is a good opportunity for you to consider the amount of feed and the characteristics of your product. Research shows that this is a great improvement.
Anti-corrosion requirements: Steel will rust, aluminum alloy will corrode, and copper will corrode. Our processing fluids can have antiseptic functions, but they cannot be rooted. We can only guarantee them within a certain period of time.
The effectiveness of the current products used: This is mainly to learn from the strengths and weaknesses, the advantages of the existing products we can retain, the shortcomings we need to improve.
Before and after the processing technology: This is related to us? Of course, the residue of the preceding processing may affect the function of our processing fluid. Also, our processing fluid is likely to affect the function of the products used in the subsequent processing.
Working environment: Our processing fluids are the same as humans. Lifespans in a good environment are not the same as those in harsh environments. Of course, we can make targeted adjustments. Just like wearing a mask, we know that it is hazy weather.
Storage conditions: Many active ingredients of the processing fluid are very sensitive to external environmental factors. We must first understand the minimum storage environment to avoid non-combat reductions.
Customer's special requirements: Sometimes customers will ask for special processing requirements. We need to listen to the customer's wishes as much as possible. This will help us to continuously improve our fluids.
Seals Rings, Corrosion Resistance Seal Rings,carbide circle ring
Zigong MT Cemented Carbide Tech Co., Ltd. , https://www.mtcarbide.com