MIM material | Density g/cm3 | Hardness | Tensile Strengh(Mpa) | Elongation% | |
Stainless Steel | 420A(HT) | ≥7.3 | ≥48HRC | ≥1600 | ≥2 |
440NB | ≥7.6 | ≥750HV | / | / | |
304L | ≥7.8 | ≥120 HV | ≥180 | ≥30 | |
316L | ≥7.9 | ≥120 HV | ≥180 | ≥40 | |
17-4PH | ≥7.6 | 320 HV | ≥660 | ≥3 | |
Iron-based alloy | Fe2Ni06C | ≥7.5 | ≤220HV | ≤300 | ≤8 |
Fe8Ni | ≥7.5 | ≤140HV | ≤210 | ≤20 | |
Fe8Ni(HT) | ≥7.5 | ≥400HV | ≥1100 | ≤3 | |
soft magnetic material | FeSi3 | ≥7.5 | 120~160HV | ≥300 | ≥20 |
MIM advantages
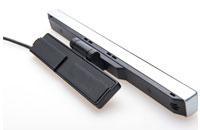
Metal Injection Molding (MIM) is an established and proven manufacturing technique for producing small, complex, tight-tolerance and high-performance metal parts. MIM is a cost-effective alternative to traditional metal forming techniques such as machining, investment casting, and powder metallurgy. MIM excels at applications that require shape complexity and material properties (high strength, magnetic permeability and corrosion resistance) that cannot be fulfilled by plastic and light metal alloys. It offers tremendous single-step parts consolidation potential that makes it a competitive alternative to stamped/machined-parts assemblies. Many design and economic limitations of traditional metalworking technologies can be readily overcome by MIM.Â
Today, MIM is serving critical performance applications in a wide range of industries and products including, automotive, commercial aerospace, cellular telephones, dental instruments, electronic heat sinks and hermetic packages, electrical connector hardware, industrial tools, fiber optic connectors, fluid spray systems, hard disk drives, pharmaceutical devices, power hand-tools, surgical instruments, and sporting equipment.
Why mim is best choice?
Cost Effective Design Flexibility
- Allows the freedom to manufacture complicated shapes that would be considered cost prohibitive by other methods.
- Provides for the manufacture of micro-sized parts in high volumes.
- Capable of producing features that cannot be achieved by investment casting such as small holes, thin walls and fine surface detail.
- Achieves net shape features such as internal and external threads, profiled holes and finely detailed surface textures, knurling, engravings and markings.
- Production scalability that allows from thousands to millions of parts, quickly and efficiently.
- Superior strength, magnetic, and corrosion properties due to high density achieved when compared to conventional powdered metal, plastics and die-casting.
- Net shape components from otherwise hard to process materials like Superalloys, Tungsten alloys and Titanium.
- Isotropic and homogeneous microstructure for uniform material properties.
- Capability to create alloys that are not available in wrought or cast form.
- Ability to make engineered density materials for weight critical applications.
About MIMO
 Suzhou Mimo Metal Technology Co.,Ltd. founded in 2006, is   located in the beautiful Yangtze River delta - Suzhou Wujiang. Company covers an area 9500 square meters, owns mixing workshop, injection molding workshop, degreasing sintering workshop, testing center. Company has always adhere to the "scientific and technological innovation, cooperation and win-win, sincere and high efficiency, first-class service" for the service concept, use high-tech enterprises and brand building our company's future, we have professional team and mature technology, resolved to become a domestic leading professional MIM manufacturing company
Our Service |
|
FAQ
Q: What's MIM process?
A: MIM (Metal Injection Molding) is a manufacturing technology that combines the shape making complexity of Plastic Injection Molding with the material flexibility of Powder Metallurgy.
Q: What's the Characteristics of MIM?
A: As a near net forming technology for manufacturing high quality precision parts, MIM has the advantages of conventional and machining methods. MIM can make a lot of complex shape parts: such as various external cutting, thread, conical outer surface, surface knurling and so on, has more features of the parts are not to use conventional powder metallurgy method. Due to the MIM manufacturing parts almost do not need to be machined, so reducing the material consumption, the number of complex shape parts in production requirements is higher than a certain value, MIM will be more economical than machining method.
Q: Why should I choose MIM?
A: MIM excels in producing small, highly complex parts that are difficult or cost prohibitive to produce with conventional technologies such as machining or casting
Q: How do I place order?
A: First, Please help to send us the product drawing, then We will check the drawing and the price will be quoted for you about 24 workhours.
Contact with us in 24 hours.
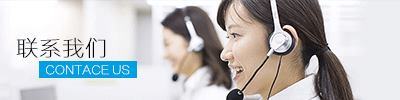
Aaron Sale of Jiangsu Mimo Metal Co.,LTD.
Â
The pipeline heat shrink coating system designed for corrosion protection of straight pipes, fittings, bends, elbows and other irregular configurations. It consists low pre-heat modified bitumen sealant adhesive and thick-wall irradiated cross linked polyolefin. When heated the backing layer shrinks and the adhesive flows and forms a reliable corrosion protection seal onto metal and adjacent coating surfaces. It cons
Heat Shrink Tape
It installed by wrapping the tape on the pipe joints ,fittings ,bends ,elbows etc .After the shrinking of the tape ,the closure patch should be installed onto the overlap of the tape.
heat shrinkable sleeves,heat shrinkable tape
Jining Xunda Pipe Coating Material Co.,Ltd , https://www.alta-altene.com