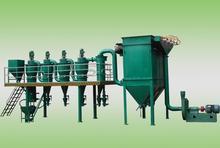
At present, there are several types of jet mills that are used industrially: flat jet mills, fluidized bed jet jet mills, circulating tube jet mills, jet jet mills, and target jet mills. Among them, the flat-type air-jet mill, the fluidized bed, the jet-type air-jet mill, and the circulating-tube air-jet mill are widely used. Now, the working principle is briefly explained:
1. As a high-pressure gas flow to smash the cavity, the flat-type air-jet mill acts as a gas distribution station for the high-pressure airflow that smashes kinetic energy into the periphery of the smashing chamber. The airflow is accelerated into a smashing grinding chamber after passing through a Laval nozzle to accelerate into a supersonic airflow, and the material flows through the Venturi nozzle. Accelerated introduction into the crushing mill cavity for simultaneous crushing. Since the Laval nozzle and the smashing chamber are installed at an acute angle, the high-speed jet stream carries animal circulation in the smashing chamber and the smashing occurs due to impacts, collisions, and friction between the granules and between the granules and the fixed target wall. The fine particles are driven into the cyclone separator at the outlet of the center of the pulverizer driven by the centripetal air flow. The coarse powder is thrown to the peripheral wall of the crushing chamber under the action of centrifugal force to make a circular motion and continue to be crushed.
2. After the fluidized bed passes through the screw feeder and enters the smashing chamber, several high-speed jets of impact energy are injected from a relatively arranged nozzle, and the airflow is rapidly expanded and the fluidized bed is suspended and boiled. , Grinding the material with friction. The coarse and fine mixed powder is driven by the negative pressure gas flow through the top of the turbine scavenging device. The fine powder is forced through the grading device and collected by the cyclone collector and the bag filter. The coarse powder is thrown by the centrifugal force generated by the gravity and the high-speed rotating grading device. To the four walls and settle back to the crushing chamber to continue smashing.
3. The raw material of the circulating tube jet mill is added into the crushing chamber by the venturi nozzle, and the high-pressure air is injected into a racetrack-shaped circulating tube crushing chamber of unequal diameter curvature through a group of nozzles to accelerate the particles to impact, collide, friction and smash. . At the same time, the swirling flow also drives the crushed particles upward into the classifying zone along the pipeline. Under the effect of the centrifugal force field in the grading zone, the dense material flow is diverted, and the fine particles are discharged after classification in the inner layer by the louver type inertial classifier. The coarse particles continue to circulate and crush along the descending tube in the outer layer.
However, at present, the most widely used fluidized bed jet-jet jet mill in the industry is designed to have a parallel and symmetrical arrangement along the inner wall of the comminution cavity, and the jet is only formed in a single plane, so the material to be crushed can only be Smashing within an approximately flat range leads to the following disadvantages:
(1) Once the material falls into the coarse material collector at the bottom of the crushing chamber, it enters the comminution blind area and cannot be further crushed;
(2) limited by the nozzle, the coarse material collector at the bottom of the smashing chamber is in the fluidization state blind zone, and the material is not fluidized, so it cannot be crushed;
(3) The crushing zone is limited by the smashing cavity, resulting in a narrow area, which reduces the probability of airflow crushing.
In response to the above problems, many research institutes and manufacturing companies have made a lot of improvements, and also applied for a large number of patents. Among them, the effect of the three-dimensional arrangement of the nozzles is the most ideal, which enlarges the crushing area and increases the collision friction probability between the material particles. Is a combination of flat and fluidized bed type of a new device, according to the performance test data, to achieve the level of similar products, under the premise of the same product and particle size, the output is significantly higher than similar products.
Pole Dance Mat,Dance Crash Mat,Pole Dance Crash Mat,Foldable Pole Dance Mats
Shaoxing geili sports and leisure goods Co.,Ltd , https://www.geilisports.com