THE ELASTOMERIC TUBE SWAGING PROCESS
This process is widely used in the commercial and military aircraft industry to fabricate tubing assemblies for hydraulic, fuel, oxygen, and similar fluid distribution systems. Â Currently, elastomeric swaging is used to fabricate tubing assemblies for both low and high pressure fluid systems made from aluminum, steel, stainless steel alloys, and titanium. Â Elastomeric swaging of end fittings produces fluid tight connections without the loss of material strength associated with thermal joining methods such as brazing and welding. Â In addition, elastomeric swaging produces high quality mechanical tube fitting attachments without the wall thinning and local stress concentrations produced by mechanical roller swaging or the older bite type designs.
In addition to serving the aerospace industry, we are now introducing our internal elastomeric swage machines and support tooling to other industries. Swagers can be used in the construction of marine engines, automobiles, trucks, refrigeration, air conditioning, motorcycles, motor homes, construction equipment, and tractors.The process is a cold forming process which utilizes extremely high radial forces applied to the internal surfaces of a tubular member to displace the tubing into grooves in an external end fitting, or into a shaped die cavity to produce tube end forms such as beads. Â The internal swaging forces are produced by the controlled linear travel of a high strength drawbolt which compresses an elastomeric expander against a static retainer ring surrounding the drawbolt. Â During the swaging cycle, controlled compression of the elastomeric material forces the tube wall radially into internal circumferential grooves in the end fitting skirt, producing a strong, leak proof mechanical attachment. Â During forming, the tube end fitting is contained within a precision matching split die cavity to provide a reactionary force to the forming operation and prevent distortion of the fitting.
Elastomeric swaging is a very rapid, efficient, and practical tube end fitting attachment process that eliminates expensive post processing operations such as radiographic or ultrasonic inspection frequently required for welded and brazed connections
We manufacture all forming dies and swage tooling for each of our elastomeric tube swagers. Pricing for these items must be quoted based on customer requirements and quantity. Each swager is equipped to comply with all applicable safety standards as well as the electrical compatibility requested by the customer. An operation and safety training package is included with each swager purchased. A six month warranty on all parts and workmanship is included in the purchase price.
The internal elastomeric swage fittings were developed to provide a simple, yet reliable method to attach separable end fittings to rigid tubes for the demanding aerospace environment.These fittings provide a lightweight and cost effective alternative to welding, brazing, or other mechanically attached methods.
Â
Advantages of Internal Swaging
Internal swaging is a mechanical method for the attachment of fittings to tubing. This is accomplished by forming tubing outward into grooves within the fitting. The following advantages can be realized from this technique.
Â
Advantages
• No special tube end preparation (cleaning or sizing)
• Very rapid fabrication (seconds per connection)
• No X-ray inspection required
• No flushing or ball-check test required
• Reduces scrap rate
• Improved fatigue performance vs. braze
• No heat-affected zones or heat-induced distortion
• No stress-relieving required
Â
These advantages can result in significant installed cost savings.
The use of Eaton internal swage fittings is ideally compatible with CAD/CAM systems for tube assembly production. Mechanical attachment at room temperature is a plus in situations where
flammability is a concern.
Â
Fitting Features
• Fittings are made of high-strength alloys (15-5 CRES,7075 Aluminum, 6AL-4V Titanium)
• Flared fitting with machined metal sealing surface eliminates tube fl are cracking
• Flared fitting uses a 2-angle face which results in a line-contact seal allowing up to
4° angular misalignment
• Various Flareless styles are available which are compatible with all flareless systems in use today
• Lipseal fittings provide excellent sealing due to a flexible beam surface plus maximum fitting
interface clearance
• Available in sizes from 1/4"(6.35mm) through 1-1/2"(38 mm).
Â
Internal Swaging Technique
Before swaging, with drawbolt / expander assembly inserte![]() Â |
After swaging, with tube formed into fitting grooves![]() |
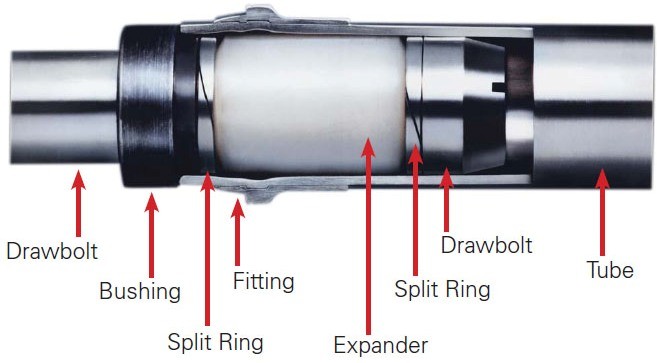
Â
THE ELASTOMERIC TUBE SWAGING PROCESS
This process is widely used in the commercial and military aircraft industry to fabricate tubing assemblies for hydraulic, fuel, oxygen, and similar fluid distribution systems. Â Currently, elastomeric swaging is used to fabricate tubing assemblies for both low and high pressure fluid systems made from aluminum, steel, stainless steel alloys, and titanium. Â Elastomeric swaging of end fittings produces fluid tight connections without the loss of material strength associated with thermal joining methods such as brazing and welding. Â In addition, elastomeric swaging produces high quality mechanical tube fitting attachments without the wall thinning and local stress concentrations produced by mechanical roller swaging or the older bite type designs.
In addition to serving the aerospace industry, we are now introducing our internal elastomeric swage machines and support tooling to other industries. Swagers can be used in the construction of marine engines, automobiles, trucks, refrigeration, air conditioning, motorcycles, motor homes, construction equipment, and tractors.The process is a cold forming process which utilizes extremely high radial forces applied to the internal surfaces of a tubular member to displace the tubing into grooves in an external end fitting, or into a shaped die cavity to produce tube end forms such as beads. Â The internal swaging forces are produced by the controlled linear travel of a high strength drawbolt which compresses an elastomeric expander against a static retainer ring surrounding the drawbolt. Â During the swaging cycle, controlled compression of the elastomeric material forces the tube wall radially into internal circumferential grooves in the end fitting skirt, producing a strong, leak proof mechanical attachment. Â During forming, the tube end fitting is contained within a precision matching split die cavity to provide a reactionary force to the forming operation and prevent distortion of the fitting.
Elastomeric swaging is a very rapid, efficient, and practical tube end fitting attachment process that eliminates expensive post processing operations such as radiographic or ultrasonic inspection frequently required for welded and brazed connections
We manufacture all forming dies and swage tooling for each of our elastomeric tube swagers. Pricing for these items must be quoted based on customer requirements and quantity. Each swager is equipped to comply with all applicable safety standards as well as the electrical compatibility requested by the customer. An operation and safety training package is included with each swager purchased. A six month warranty on all parts and workmanship is included in the purchase price.
The internal elastomeric swage fittings were developed to provide a simple, yet reliable method to attach separable end fittings to rigid tubes for the demanding aerospace environment.These fittings provide a lightweight and cost effective alternative to welding, brazing, or other mechanically attached methods.
Â
Advantages of Internal Swaging
Internal swaging is a mechanical method for the attachment of fittings to tubing. This is accomplished by forming tubing outward into grooves within the fitting. The following advantages can be realized from this technique.
Â
Advantages
• No special tube end preparation (cleaning or sizing)
• Very rapid fabrication (seconds per connection)
• No X-ray inspection required
• No flushing or ball-check test required
• Reduces scrap rate
• Improved fatigue performance vs. braze
• No heat-affected zones or heat-induced distortion
• No stress-relieving required
Â
These advantages can result in significant installed cost savings.
The use of Eaton internal swage fittings is ideally compatible with CAD/CAM systems for tube assembly production. Mechanical attachment at room temperature is a plus in situations where
flammability is a concern.
Â
Fitting Features
• Fittings are made of high-strength alloys (15-5 CRES,7075 Aluminum, 6AL-4V Titanium)
• Flared fitting with machined metal sealing surface eliminates tube fl are cracking
• Flared fitting uses a 2-angle face which results in a line-contact seal allowing up to
4° angular misalignment
• Various Flareless styles are available which are compatible with all flareless systems in use today
• Lipseal fittings provide excellent sealing due to a flexible beam surface plus maximum fitting
interface clearance
• Available in sizes from 1/4"(6.35mm) through 1-1/2"(38 mm).
Â
Internal Swaging Technique
Before swaging, with drawbolt / expander assembly inserte![]() Â |
After swaging, with tube formed into fitting grooves![]() |
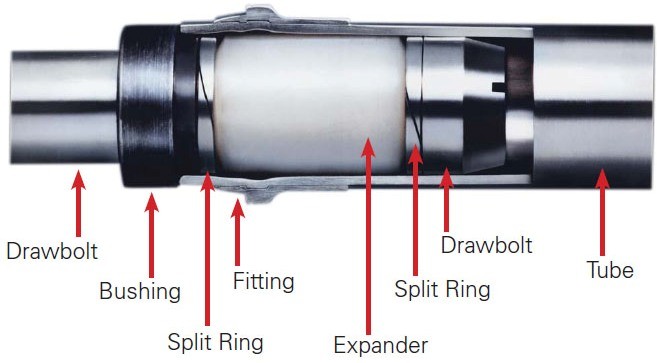
Â
Mitsubishi Diesel Generators :
·Engine and alternator shall be mounted on a same frame steel skid.
·Built-in damper for anti-vibration.·Small size, low weight, easy to operating, installation and maintenance.
·World most famous brand diesel engine: Mitsubishi Engine
·World famous brand AC alternator: Stamford, MeccAlte, Leroy Somer, etc
·Advanced and reliable controller: Auto Start AMF & Remote control by PC with RS232/485
·Full range protect function and alarm shutdown feature.
·Comply with ISO8528 national standard and ISO9001 quality standard.
Mitsubishi Diesel generator,Mitsubishi diesel genset,Mitsubishi genset,Mitsubishi generator,Mitsubishi diesel engine
Guangdong Superwatt Power Equipment Co., Ltd , https://www.swtgenset.com